Description
PETROL STEEL uses high-precision CNC machining and friction stir welding (FSW) technology to produce various liquid-cooled radiators/cold plates, and Liquid Cooling Solutions Aluminum Liquid Cooling Plates. PETROL STEEL Friction stir welding (FSW) technology provides solid joints with mechanical properties similar to the base material, thus forming an overall structure and realizing a very strong seal. High-performance heat sinks provide an efficient way to manage electronic systems with highly concentrated power and heat.
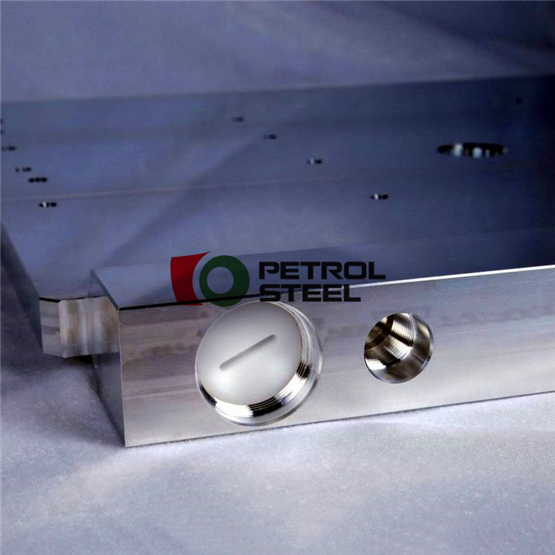
As the professional Liquid Cooling Solutions Aluminum Liquid Cooling Plates supplier, PETROL STEEL CO., LTD is good at advanced thermal solutions. We have a special engineering team full of experience, and we can develop different cold plates for equipment like EV, Locomotives, SVC, IGBT, 3C applications.
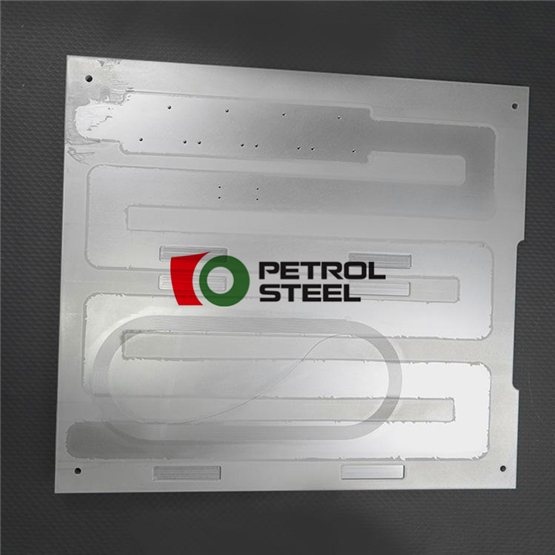
Our Liquid Cooling Solutions Aluminum Liquid Cooling Plates are used for: Transportation, Electric locomotive, Electricity, Energy, Wind power, Photovoltaic, Electric Vehicle, Bullet train, Frequency converter, Control cabinets, Medical Industry, 3C products. Our battery cold plates are applied for electrical vehicles, cool down the battery, widely applied for cooling down the electrical component in the control cabinet. The aeronautics astronautics cold plates are applied for all kinds of trains, control valves, and other air-driven components.
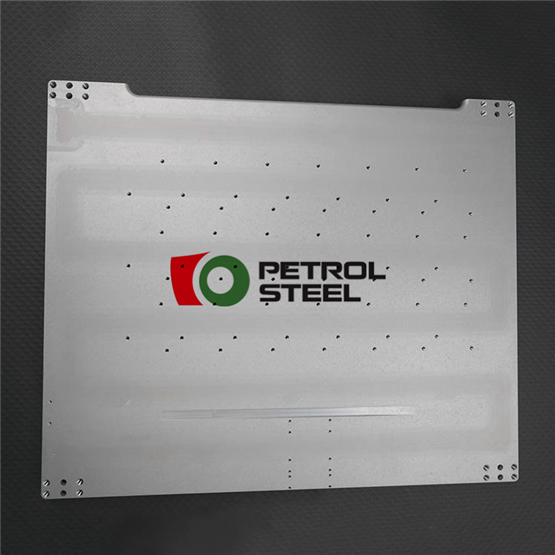
The water-cooled radiator which is made of Liquid Cooling Solutions Aluminum Liquid Cooling Plates is a high-efficiency radiator for power components such as IGBT and GTO, which control the temperature of the power module. The water-cooling plate is a high-efficiency radiator for power components such as IGBT and GTO. It controls the temperature of the power module so that it does not exceed the maximum temperature specified by the standards and specifications under the working environment conditions. The allowable temperature calculation is based on finite element heating. The analysis is based on the analysis of the working conditions of the components and is consistent with the reliability requirements of the product and the requirements of the use environment. So as to achieve the safe, stable, and reliable operation of the power module and prolong the service life of the equipment.
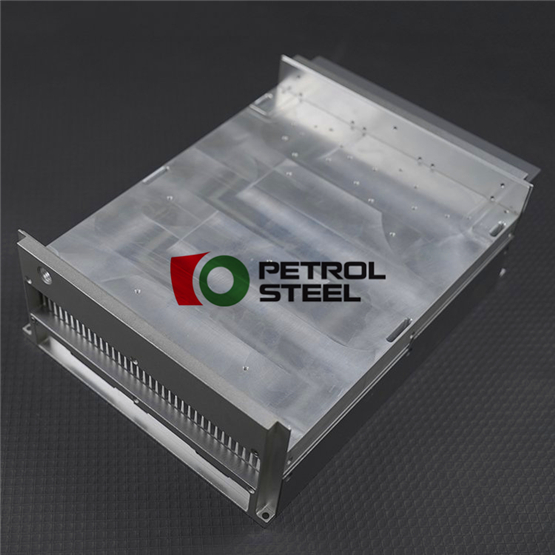
The Product parameter of PETROL STEEL Liquid Cooling Solutions Aluminum Liquid Cooling Plates
Size: length * width * thickness: 1,250*800*60mm,
Surface treatment: cleaning, black anode, nickel plating,
Flatness: <0.05(100×100),
Roughness: <1.6μm,
Joint method: vacuum brazing or argon arc welding,
Coolant temperature (°C): minus 30°C to 60°C,
Coolant: pure water or a mixture of water and ethylene glycol,
Flow rate: <80L/min,
The surface temperature rise of the liquid cold plate (℃): <30℃,
The upper limit of working pressure (kPa): 0.6Mpa---3.0MPa,
Calorific value: <30kW,
Thermal resistance: <2℃/kw (according to heat source distribution),
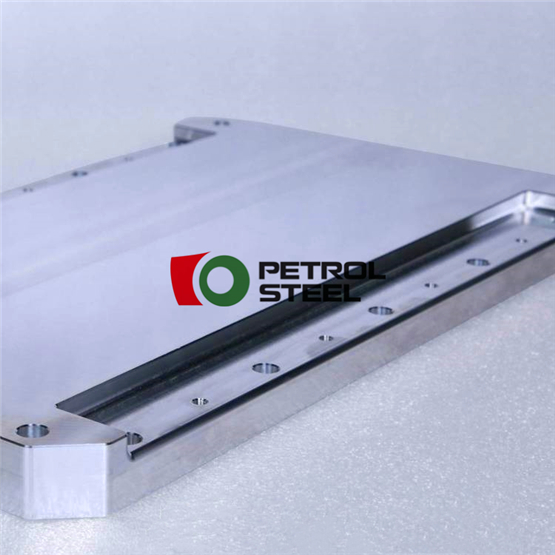
Applications of our Liquid Cooling Solutions Aluminum Liquid Cooling Plates are as the followings:
Transportation: electric locomotives, high-speed trains, electric drive ships, electric vehicles, etc,
Power transmission: UHV DC transmission, flexible DC, transmission, etc,
New energy: wind power, photovoltaic power generation, etc,
Others: industrial frequency conversion, signal processing, UPS, medical, laser, etc.
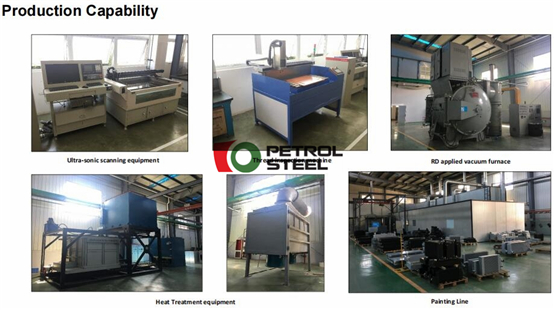
Liquid Cooling Solutions Aluminum Liquid Cooling Plates: For Engine, Cooling system for generator, converter or other equipment, etc.
Oil Coolers plate: For Hydraulic system, Lubrication system, Gearbox, Fuel cooler, etc.
Charge Air Cooler plate, After Cooler: For Engine, Air compressors, Natural gas, etc.
Combined cooler plate: Cool multi-medium in the same cooler.
Cold plate, Air duct plate: Cool down the electric elements in some control cabinet, for SVC, IGBT, etc.
Air duct plate: Connecting air valves, switches, gauges, etc.
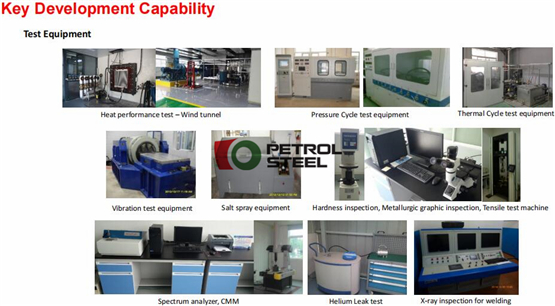
Scope of application of our Liquid Cooling Solutions Aluminum Liquid Cooling Plates are the followings for reference.
1. Transportation: electric locomotives, railways, electric-powered ships, electric vehicles, etc,
2. Smart grid UHV DC, VSC-HVDC, etc,
3. New energy, wind power converter, photovoltaic converter, etc,
4. Inverter, signal processing, UPS, medical equipment, laser, and other industries.
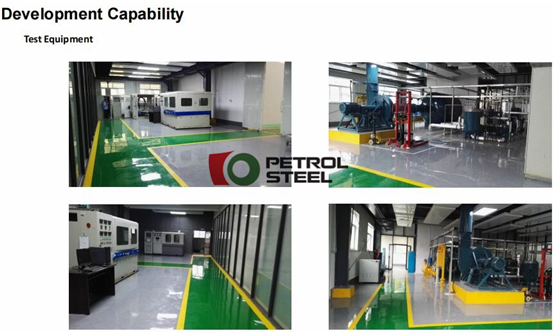
Our company manufactures a series of aluminum profiles from mold manufacturing, aluminum profile extrusion, aluminum surface treatment, aluminum CNC processing, stamping, bending, sawing, welding, and so on. Products are used in construction, transportation, machinery, electronic and electrical, automobiles, ships, subways, and other fields.
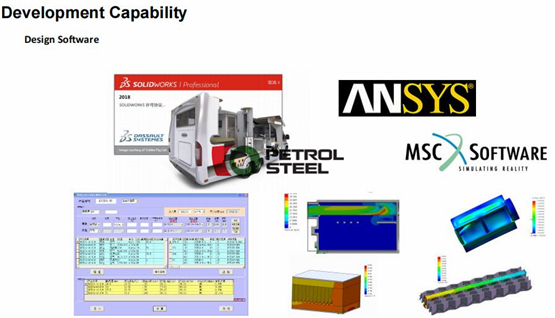
Friction stir welding FSW is a solid-state welding method of Liquid Cooling Solutions Aluminum Liquid Cooling Plates. Under the action of constant pressure or incremental pressure and torque, the relative movement between the welding contact end faces is used to generate frictional heat and plastic deformation heat on the friction surface and its vicinity, so that the temperature of the nearby area rises to close (generally lower than ) The temperature of the melting point. The deformation resistance of the material is reduced, the plasticity is improved, and the oxide film at the interface is broken. Under the action of the upsetting pressure, the material is plastically deformed and flowed, and the molecular diffusion and recrystallization of the interface are used to realize the solid-state welding method of welding.
Friction stir welding FSW usually consists of the following four steps:
1. Convert mechanical energy into heat;
2. Plastic deformation of materials;
3. Forging pressure under thermoplasticity;
4. Diffusion and recrystallization between molecules.
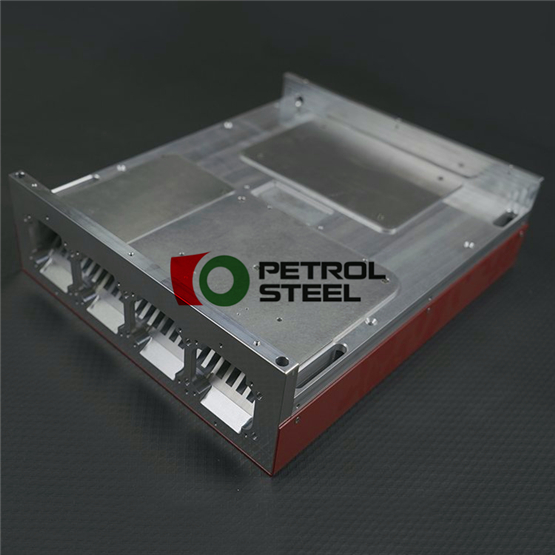
Why choose the friction stir welding FSW process on Liquid Cooling Solutions Aluminum Liquid Cooling Plates?
1. Compared with the traditional buried copper pipe water-cooling plate, the friction stir welding water-cooling plate has a larger flow channel, which can further reduce the thermal resistance. Especially in the use of complex runners and runners with high and low differences, the friction stir welding process water-cooled plate is more flexible.
2. Compared with the traditional assembled screw fixed water-cooling plate, the friction stir welding water-cooling plate has a more stable heat dissipation performance.
3. Compared with brazing water-cooled plates, friction stir welding has a simpler welding process, higher production efficiency, higher weld strength, and can avoid problems such as pores and liquid leakage in high-temperature fusion welding.
4. If the industrial radiator adopts the friction welding process, it can solve the technical bottleneck of high multiples and ultra-wide profiles. If two or more profiles are used for splicing, it can be easily made into ultra-wide structure, high-density profile products, and the mold cost is low, the delivery time is short, and the performance is reliable.
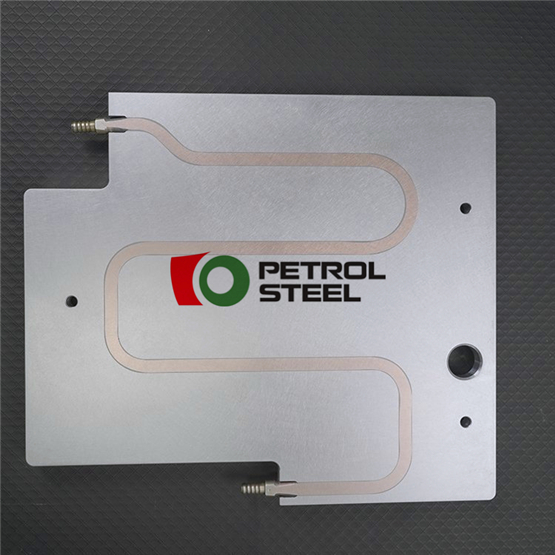
Our Service form: processing with supplied materials or drawings, non-standard customization; Welding method: vacuum brazing, Friction stir welding FSW; Types of aluminum materials: 1 series, 3 series, 6 series aluminum alloys and any combination of the above two; Heat dissipation structure: shovel tooth form, forged copper pillar form, CNC machining runner and other forms; Test methods: air pressure test, water pressure test, helium leak test, ultrasonic test, etc.; Technical advantages: low deformation rate, high mechanical strength, uniform, and beautiful welds, no flux, strong corrosion-resistance, mass production, non-standard customization, short production cycle; Value-added services: structural design optimization, production process design, reliability analysis.
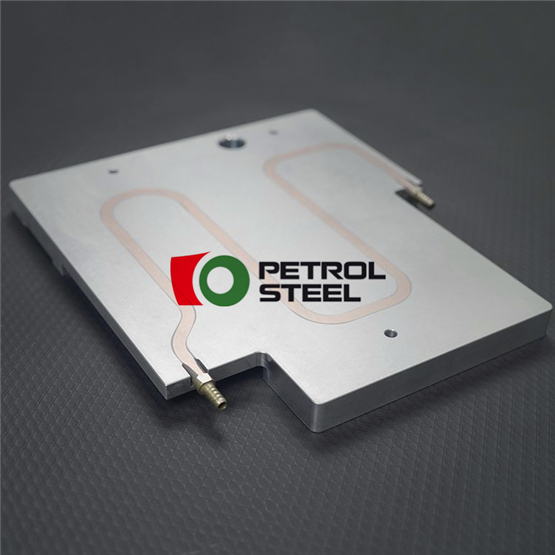
The radiator can be made of copper alloy plates or aluminum alloy plates, with a surface treatment such as copper plating or aluminum nickel plating, or aluminum anodizing. The tests include X-ray inspection of welding quality, leak test, flow resistance test, thermal resistance test, temperature rise test under different powers, radiator efficiency test, and radiator simulation test under different application conditions. Precision machined radiator body and surface, with high precision and low-pressure drop, double-sided cooling capacity, the possibility of the large radiator size, compatibility with industry-approved coolant, friction stir welding joints have good non-leakage, high-pressure rated performance, and high corrosion resistance. High-power electronics, lasers equipment, power drives, medical equipment, military, and aerospace industries.
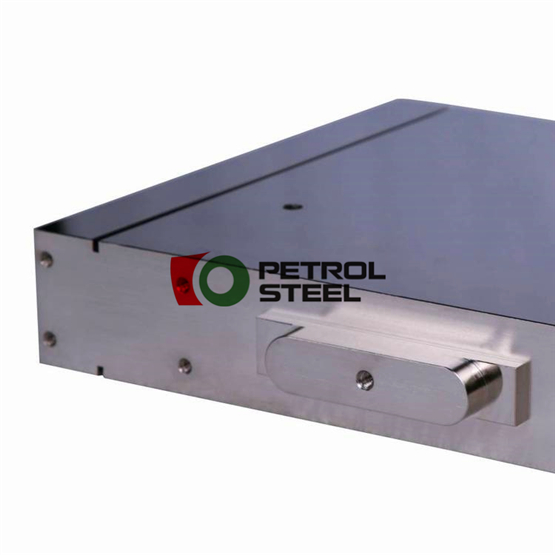
The drilled aluminum cold plate is processed into a copper tube or a stainless steel tube, and it is embedded in the water pipe CNC profile processing. It has the characteristics of simple technology, low mass production cost, and poor performance.
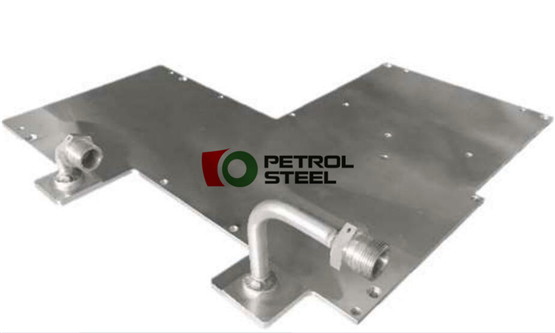
The pressure tube aluminum cold plate is processed by milling grooves or profile drawing grooves, and the bent copper pipes are embedded in the grooves through welding, pressing, and pasting. CNC contour processing has the characteristics of simple technology, low mass production cost, and poor performance. The assembled aluminum cold plate is processed into CNC or die-casting water chamber, body shape, and cover. Using a screw and sealing ring or glue to seal, the process is simple, the cost is low, the performance is medium, and the reliability is low.
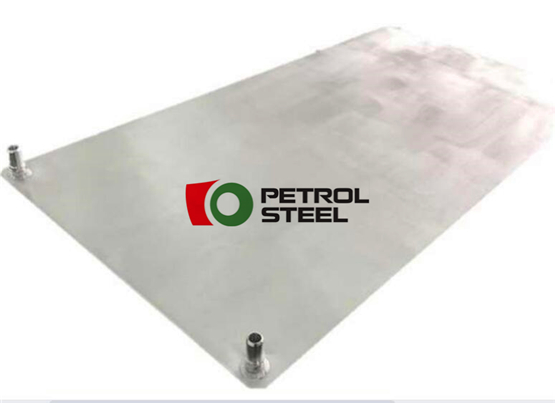
Friction welding electron beam welding Liquid Cooling Solutions Aluminum Liquid Cooling Plates adopt numerical control processing water chamber and cover plate. Friction welding or electron beam welding is used for hermetic welding. CNC machining finished product. The process is more complicated, the structure is flexible, the performance is good, the reliability is high, and the cost is relatively high.The vacuum brazing aluminum cold plate is processed by numerical control or other methods in the water chamber. The end face is sealed by vacuum brazing. It adopts CNC machining, complex technology, flexible structure, excellent performance, high reliability, and the highest cost.
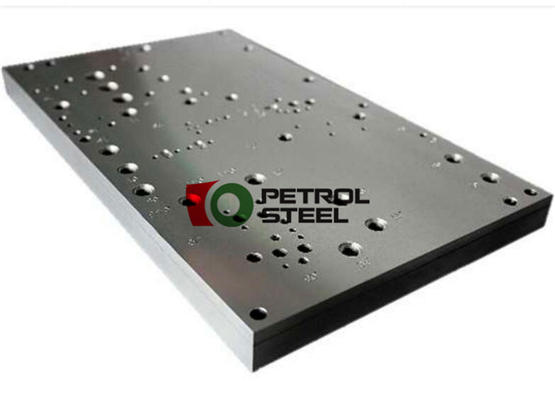
Vacuum brazing aluminum cold plate, Aluminum Alloy Liquid Cooled Plate, air duct plate, Water Cooler plate, Oil Coolers plate, Charge Air Cooler plate, Air duct plate, aeronautic astronautic bar plate coolers, Vacuum brazed Water cold plate, Vacuum brazed Air channel plate, Liquid-cooled cold plate, Water Cooled Heat Sink, Copper vacuum brazing liquid-cooled plate, Aluminum uniform temperature plate processing, aluminum alloy vacuum brazing manufacturer, liquid-cooled plate aluminum alloy vacuum brazing for new energy vehicles, aluminum alloy liquid-cooled plate vacuum brazing processing plant, liquid-cooled plate aluminum alloy vacuum brazing processing plant for laser, Aluminum uniform temperature plate and aluminum alloy vacuum brazing processing, waveguide aluminum water cooling plate, liquid cooling aluminum plate processing, vacuum welding water cooling plate, lithium battery water cooling plate processing, waveguide water cooling plate, ultra-thin optical fiber water cooling plate, liquid cooling plate, friction stir welding processing, new energy vehicle water cooling plate, aluminum alloy water cooling plate forging processing, waveguide aluminum water cooling plate, liquid cooling aluminum plate processing, vacuum welding water cooling plate, new energy vehicle heat dissipation water cooling plate processing, FSW friction stir welding process, Water-cooling plate radiator, solving the process of heat dissipation, friction stir welding water-cooling plate, black anodized CNC precision processing, aluminum alloy water-cooled heat dissipation base plate, CNC computer gong friction stir welding processing, thermal fiber ultra-thin water-cooling plate processing, solid-state welding friction welding Water-cooling plate production, radiator processing, CNC processing, large ultra-thin optical fiber water-cooling plate, friction stir welding processing of heat dissipation plate, liquid cooling plate, friction welding heat pipe, water cooling radiator, water cooling plate customization, cooling solutions, water cooling plate customization processing, Aluminum 6061 laser housing, industrial control cavity structure.
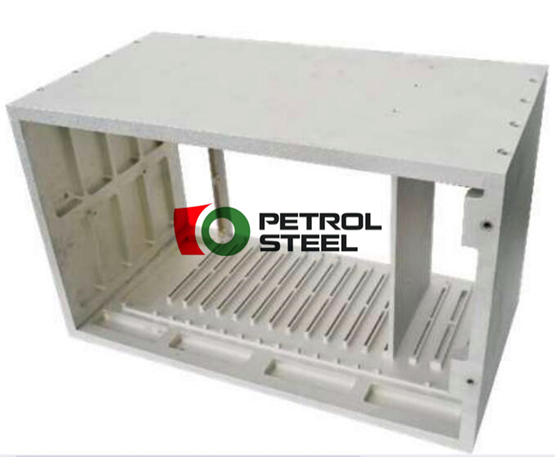
Forced Convection Type Extrusion Heatsink Thermal Solution, CrossCut Extrusion Aluminum Heat Sink Solution, Solar Energy converter Heat Sink Thermal Solution,Double Side IGBT Heat Sink Solution Swaged Process, FSW Friction Stir Welding Process Aluminum Contact, High Fins Desity Extrusion Heat Sinks,Big Heat Sink With Heat Pipes Thermal Solution, Big Aluminum Extrusion Fins Heat Sink, Aluminum Extrusion Swage Process High Fin Density Solution, FSW & CMT Aluminum extrusion battery case details, FSW CMT Al extrusion battery cage,high reliability integrated liquid cold plate, FSW Process LCP, Brazing Process Liquide cold plate, EV battery thermal solution, Friction Stir Welding Process For Laser Projector Liquid Cold Plate, 1200W Laser Heat Source Thermal Solution,800W 1200W Lase Thermal Cooling solution, Friction Stir Welding, Big Aluminum Plate With Copper Tube Solution, New Energy Car IGBT Heatsink Thermal Solution,Small Liquid Cold Plate With copper Pipes, Aluminum 6063 base Liquid Cold Plate, Copper Pipes With Aluminum Base With High Press Process Contact,Brazing Aluminum Liquid Cold Plate Thermal Solution,Liquid Cold Plate With Aluminum Extrusion and Deep Holes, LCP Manufacturer In China,Circulation Water Plate With Copper Pipes And Aluminum Base, Telecom RRU Heat Sink Solution, Industrial IGBT TO 220 IC High Power Solution,Industrial Electronics Big Power Thermal Solution, Aluminum Fins With Heat Pipes Copper Base Heatsink Supplier, Aluminum Base With Copper Heatpipes Heat Sink, High PowerIGBT Heat Sink FSW Process Thermal Solution, Copper Fin With Heat Pipes Copper Base Soldering Process, Transportation IGBT Electronics Thermal Solution, PowerConversion IGBT Heat Sink,CPU Server 2U Heat Sink Thermal, CNC Lathe Machining For Aluminum,CNC Case Aluminum Cold Plate, Extrusion CNC Machining Cold Plate,low cost and high-performance heat sink solution, LED High Power Street Lamp Aluminum Extrusion Profile, Transportation IGBT Heat Sink Solution, IGBT Semiconductor Thermal Solution, CNC High Precision Aluminum Heat.
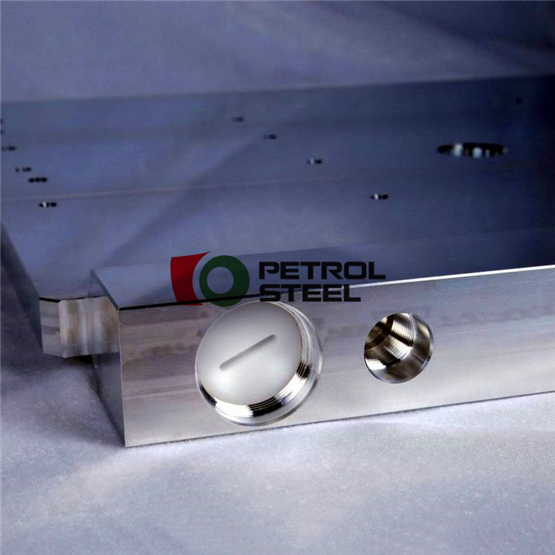
As the professional Liquid Cooling Solutions Aluminum Liquid Cooling Plates supplier, PETROL STEEL CO., LTD is good at advanced thermal solutions. We have a special engineering team full of experience, and we can develop different cold plates for equipment like EV, Locomotives, SVC, IGBT, 3C applications.
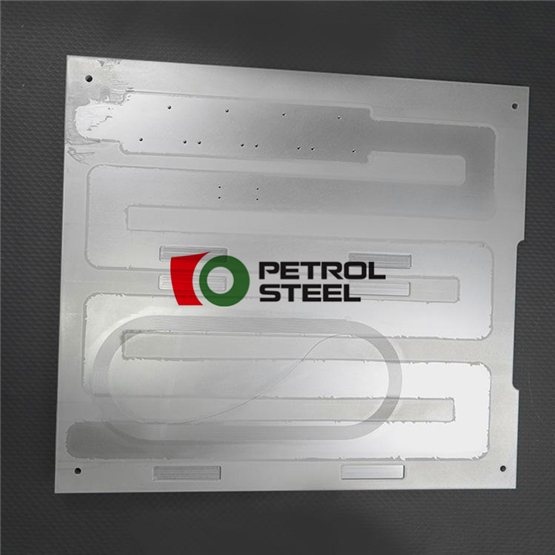
Our Liquid Cooling Solutions Aluminum Liquid Cooling Plates are used for: Transportation, Electric locomotive, Electricity, Energy, Wind power, Photovoltaic, Electric Vehicle, Bullet train, Frequency converter, Control cabinets, Medical Industry, 3C products. Our battery cold plates are applied for electrical vehicles, cool down the battery, widely applied for cooling down the electrical component in the control cabinet. The aeronautics astronautics cold plates are applied for all kinds of trains, control valves, and other air-driven components.
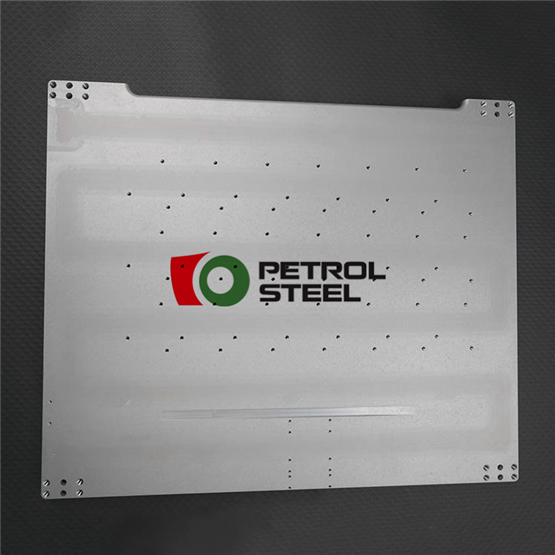
The water-cooled radiator which is made of Liquid Cooling Solutions Aluminum Liquid Cooling Plates is a high-efficiency radiator for power components such as IGBT and GTO, which control the temperature of the power module. The water-cooling plate is a high-efficiency radiator for power components such as IGBT and GTO. It controls the temperature of the power module so that it does not exceed the maximum temperature specified by the standards and specifications under the working environment conditions. The allowable temperature calculation is based on finite element heating. The analysis is based on the analysis of the working conditions of the components and is consistent with the reliability requirements of the product and the requirements of the use environment. So as to achieve the safe, stable, and reliable operation of the power module and prolong the service life of the equipment.
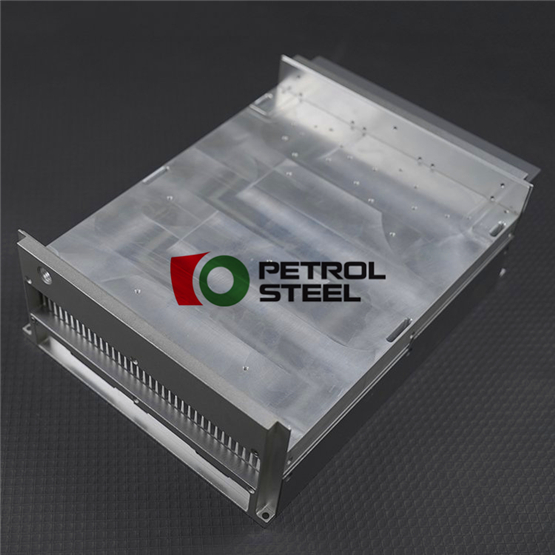
The Product parameter of PETROL STEEL Liquid Cooling Solutions Aluminum Liquid Cooling Plates
Size: length * width * thickness: 1,250*800*60mm,
Surface treatment: cleaning, black anode, nickel plating,
Flatness: <0.05(100×100),
Roughness: <1.6μm,
Joint method: vacuum brazing or argon arc welding,
Coolant temperature (°C): minus 30°C to 60°C,
Coolant: pure water or a mixture of water and ethylene glycol,
Flow rate: <80L/min,
The surface temperature rise of the liquid cold plate (℃): <30℃,
The upper limit of working pressure (kPa): 0.6Mpa---3.0MPa,
Calorific value: <30kW,
Thermal resistance: <2℃/kw (according to heat source distribution),
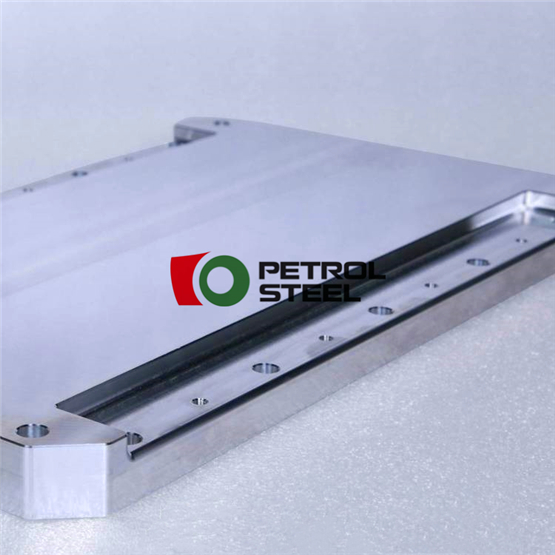
Applications of our Liquid Cooling Solutions Aluminum Liquid Cooling Plates are as the followings:
Transportation: electric locomotives, high-speed trains, electric drive ships, electric vehicles, etc,
Power transmission: UHV DC transmission, flexible DC, transmission, etc,
New energy: wind power, photovoltaic power generation, etc,
Others: industrial frequency conversion, signal processing, UPS, medical, laser, etc.
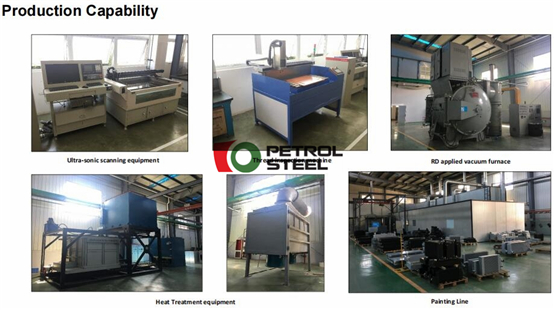
Liquid Cooling Solutions Aluminum Liquid Cooling Plates: For Engine, Cooling system for generator, converter or other equipment, etc.
Oil Coolers plate: For Hydraulic system, Lubrication system, Gearbox, Fuel cooler, etc.
Charge Air Cooler plate, After Cooler: For Engine, Air compressors, Natural gas, etc.
Combined cooler plate: Cool multi-medium in the same cooler.
Cold plate, Air duct plate: Cool down the electric elements in some control cabinet, for SVC, IGBT, etc.
Air duct plate: Connecting air valves, switches, gauges, etc.
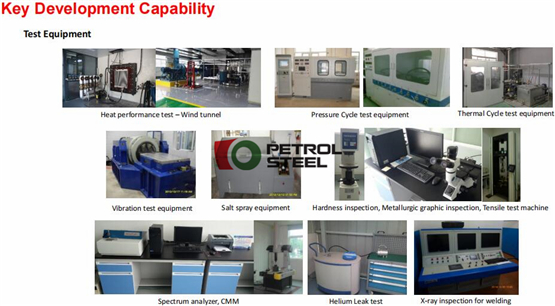
Scope of application of our Liquid Cooling Solutions Aluminum Liquid Cooling Plates are the followings for reference.
1. Transportation: electric locomotives, railways, electric-powered ships, electric vehicles, etc,
2. Smart grid UHV DC, VSC-HVDC, etc,
3. New energy, wind power converter, photovoltaic converter, etc,
4. Inverter, signal processing, UPS, medical equipment, laser, and other industries.
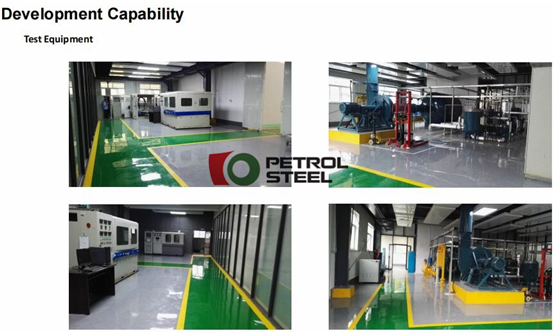
Our company manufactures a series of aluminum profiles from mold manufacturing, aluminum profile extrusion, aluminum surface treatment, aluminum CNC processing, stamping, bending, sawing, welding, and so on. Products are used in construction, transportation, machinery, electronic and electrical, automobiles, ships, subways, and other fields.
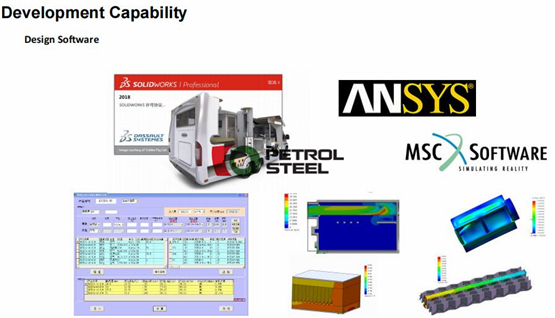
Friction stir welding FSW is a solid-state welding method of Liquid Cooling Solutions Aluminum Liquid Cooling Plates. Under the action of constant pressure or incremental pressure and torque, the relative movement between the welding contact end faces is used to generate frictional heat and plastic deformation heat on the friction surface and its vicinity, so that the temperature of the nearby area rises to close (generally lower than ) The temperature of the melting point. The deformation resistance of the material is reduced, the plasticity is improved, and the oxide film at the interface is broken. Under the action of the upsetting pressure, the material is plastically deformed and flowed, and the molecular diffusion and recrystallization of the interface are used to realize the solid-state welding method of welding.
Friction stir welding FSW usually consists of the following four steps:
1. Convert mechanical energy into heat;
2. Plastic deformation of materials;
3. Forging pressure under thermoplasticity;
4. Diffusion and recrystallization between molecules.
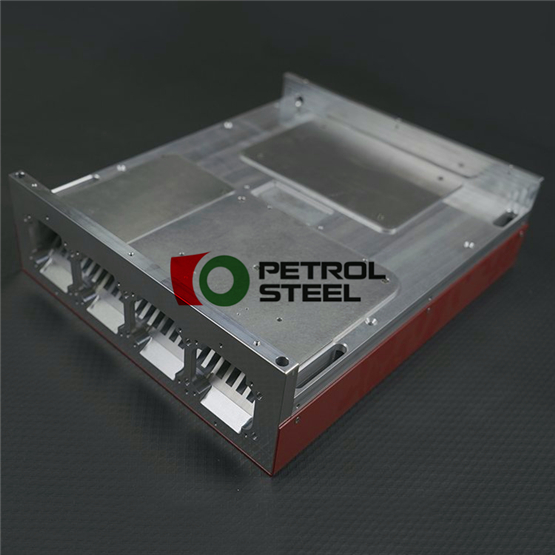
Why choose the friction stir welding FSW process on Liquid Cooling Solutions Aluminum Liquid Cooling Plates?
1. Compared with the traditional buried copper pipe water-cooling plate, the friction stir welding water-cooling plate has a larger flow channel, which can further reduce the thermal resistance. Especially in the use of complex runners and runners with high and low differences, the friction stir welding process water-cooled plate is more flexible.
2. Compared with the traditional assembled screw fixed water-cooling plate, the friction stir welding water-cooling plate has a more stable heat dissipation performance.
3. Compared with brazing water-cooled plates, friction stir welding has a simpler welding process, higher production efficiency, higher weld strength, and can avoid problems such as pores and liquid leakage in high-temperature fusion welding.
4. If the industrial radiator adopts the friction welding process, it can solve the technical bottleneck of high multiples and ultra-wide profiles. If two or more profiles are used for splicing, it can be easily made into ultra-wide structure, high-density profile products, and the mold cost is low, the delivery time is short, and the performance is reliable.
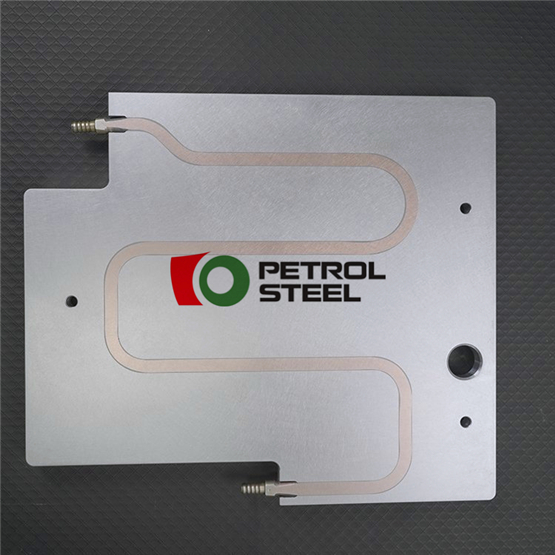
Our Service form: processing with supplied materials or drawings, non-standard customization; Welding method: vacuum brazing, Friction stir welding FSW; Types of aluminum materials: 1 series, 3 series, 6 series aluminum alloys and any combination of the above two; Heat dissipation structure: shovel tooth form, forged copper pillar form, CNC machining runner and other forms; Test methods: air pressure test, water pressure test, helium leak test, ultrasonic test, etc.; Technical advantages: low deformation rate, high mechanical strength, uniform, and beautiful welds, no flux, strong corrosion-resistance, mass production, non-standard customization, short production cycle; Value-added services: structural design optimization, production process design, reliability analysis.
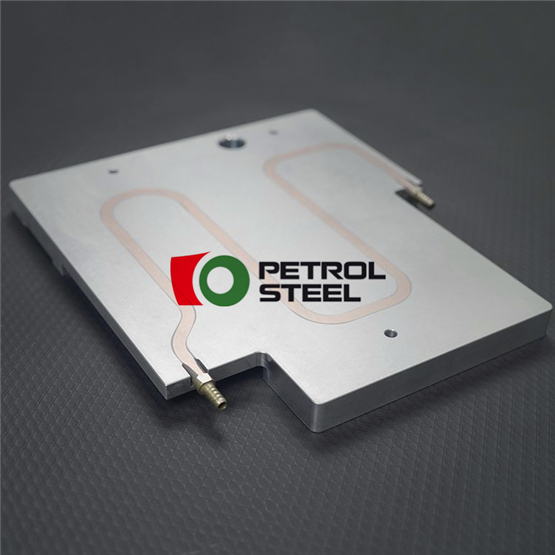
The radiator can be made of copper alloy plates or aluminum alloy plates, with a surface treatment such as copper plating or aluminum nickel plating, or aluminum anodizing. The tests include X-ray inspection of welding quality, leak test, flow resistance test, thermal resistance test, temperature rise test under different powers, radiator efficiency test, and radiator simulation test under different application conditions. Precision machined radiator body and surface, with high precision and low-pressure drop, double-sided cooling capacity, the possibility of the large radiator size, compatibility with industry-approved coolant, friction stir welding joints have good non-leakage, high-pressure rated performance, and high corrosion resistance. High-power electronics, lasers equipment, power drives, medical equipment, military, and aerospace industries.
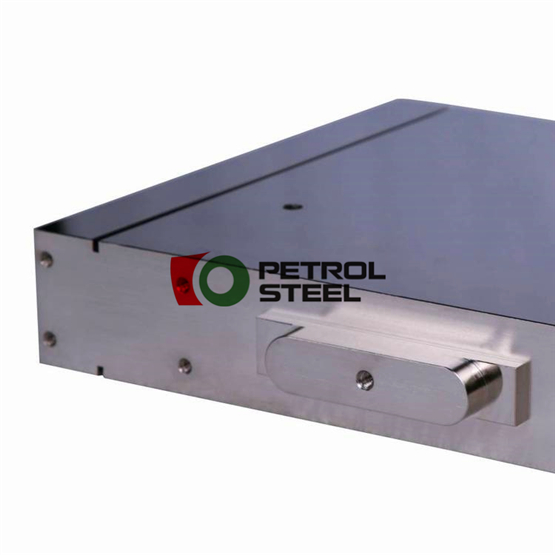
The drilled aluminum cold plate is processed into a copper tube or a stainless steel tube, and it is embedded in the water pipe CNC profile processing. It has the characteristics of simple technology, low mass production cost, and poor performance.
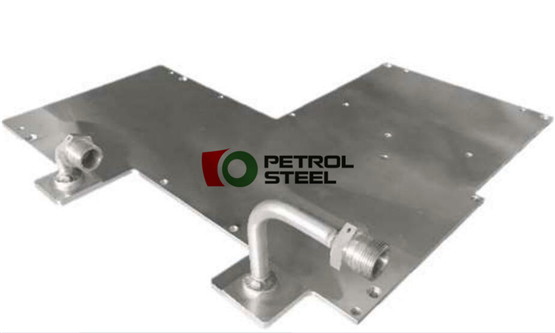
The pressure tube aluminum cold plate is processed by milling grooves or profile drawing grooves, and the bent copper pipes are embedded in the grooves through welding, pressing, and pasting. CNC contour processing has the characteristics of simple technology, low mass production cost, and poor performance. The assembled aluminum cold plate is processed into CNC or die-casting water chamber, body shape, and cover. Using a screw and sealing ring or glue to seal, the process is simple, the cost is low, the performance is medium, and the reliability is low.
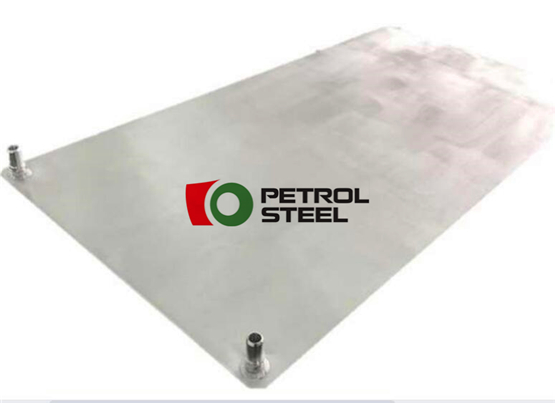
Friction welding electron beam welding Liquid Cooling Solutions Aluminum Liquid Cooling Plates adopt numerical control processing water chamber and cover plate. Friction welding or electron beam welding is used for hermetic welding. CNC machining finished product. The process is more complicated, the structure is flexible, the performance is good, the reliability is high, and the cost is relatively high.The vacuum brazing aluminum cold plate is processed by numerical control or other methods in the water chamber. The end face is sealed by vacuum brazing. It adopts CNC machining, complex technology, flexible structure, excellent performance, high reliability, and the highest cost.
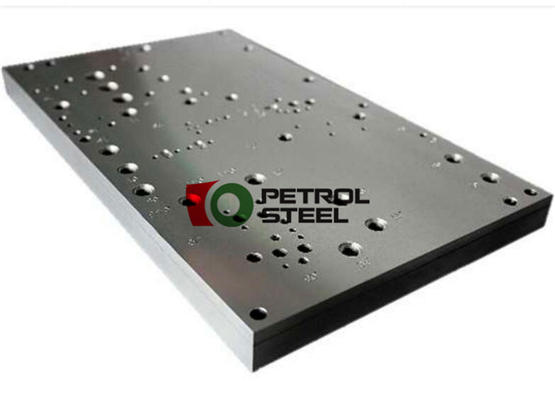
Vacuum brazing aluminum cold plate, Aluminum Alloy Liquid Cooled Plate, air duct plate, Water Cooler plate, Oil Coolers plate, Charge Air Cooler plate, Air duct plate, aeronautic astronautic bar plate coolers, Vacuum brazed Water cold plate, Vacuum brazed Air channel plate, Liquid-cooled cold plate, Water Cooled Heat Sink, Copper vacuum brazing liquid-cooled plate, Aluminum uniform temperature plate processing, aluminum alloy vacuum brazing manufacturer, liquid-cooled plate aluminum alloy vacuum brazing for new energy vehicles, aluminum alloy liquid-cooled plate vacuum brazing processing plant, liquid-cooled plate aluminum alloy vacuum brazing processing plant for laser, Aluminum uniform temperature plate and aluminum alloy vacuum brazing processing, waveguide aluminum water cooling plate, liquid cooling aluminum plate processing, vacuum welding water cooling plate, lithium battery water cooling plate processing, waveguide water cooling plate, ultra-thin optical fiber water cooling plate, liquid cooling plate, friction stir welding processing, new energy vehicle water cooling plate, aluminum alloy water cooling plate forging processing, waveguide aluminum water cooling plate, liquid cooling aluminum plate processing, vacuum welding water cooling plate, new energy vehicle heat dissipation water cooling plate processing, FSW friction stir welding process, Water-cooling plate radiator, solving the process of heat dissipation, friction stir welding water-cooling plate, black anodized CNC precision processing, aluminum alloy water-cooled heat dissipation base plate, CNC computer gong friction stir welding processing, thermal fiber ultra-thin water-cooling plate processing, solid-state welding friction welding Water-cooling plate production, radiator processing, CNC processing, large ultra-thin optical fiber water-cooling plate, friction stir welding processing of heat dissipation plate, liquid cooling plate, friction welding heat pipe, water cooling radiator, water cooling plate customization, cooling solutions, water cooling plate customization processing, Aluminum 6061 laser housing, industrial control cavity structure.
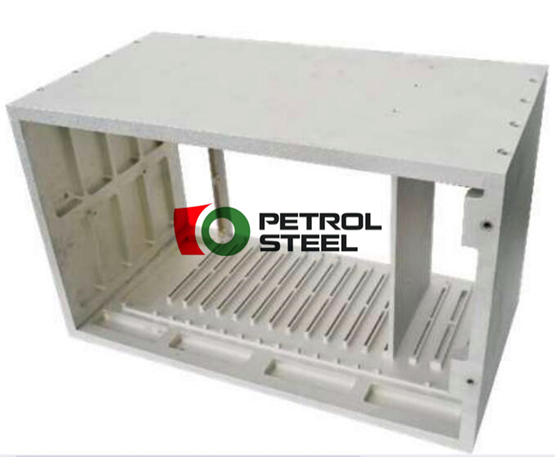
Forced Convection Type Extrusion Heatsink Thermal Solution, CrossCut Extrusion Aluminum Heat Sink Solution, Solar Energy converter Heat Sink Thermal Solution,Double Side IGBT Heat Sink Solution Swaged Process, FSW Friction Stir Welding Process Aluminum Contact, High Fins Desity Extrusion Heat Sinks,Big Heat Sink With Heat Pipes Thermal Solution, Big Aluminum Extrusion Fins Heat Sink, Aluminum Extrusion Swage Process High Fin Density Solution, FSW & CMT Aluminum extrusion battery case details, FSW CMT Al extrusion battery cage,high reliability integrated liquid cold plate, FSW Process LCP, Brazing Process Liquide cold plate, EV battery thermal solution, Friction Stir Welding Process For Laser Projector Liquid Cold Plate, 1200W Laser Heat Source Thermal Solution,800W 1200W Lase Thermal Cooling solution, Friction Stir Welding, Big Aluminum Plate With Copper Tube Solution, New Energy Car IGBT Heatsink Thermal Solution,Small Liquid Cold Plate With copper Pipes, Aluminum 6063 base Liquid Cold Plate, Copper Pipes With Aluminum Base With High Press Process Contact,Brazing Aluminum Liquid Cold Plate Thermal Solution,Liquid Cold Plate With Aluminum Extrusion and Deep Holes, LCP Manufacturer In China,Circulation Water Plate With Copper Pipes And Aluminum Base, Telecom RRU Heat Sink Solution, Industrial IGBT TO 220 IC High Power Solution,Industrial Electronics Big Power Thermal Solution, Aluminum Fins With Heat Pipes Copper Base Heatsink Supplier, Aluminum Base With Copper Heatpipes Heat Sink, High PowerIGBT Heat Sink FSW Process Thermal Solution, Copper Fin With Heat Pipes Copper Base Soldering Process, Transportation IGBT Electronics Thermal Solution, PowerConversion IGBT Heat Sink,CPU Server 2U Heat Sink Thermal, CNC Lathe Machining For Aluminum,CNC Case Aluminum Cold Plate, Extrusion CNC Machining Cold Plate,low cost and high-performance heat sink solution, LED High Power Street Lamp Aluminum Extrusion Profile, Transportation IGBT Heat Sink Solution, IGBT Semiconductor Thermal Solution, CNC High Precision Aluminum Heat.